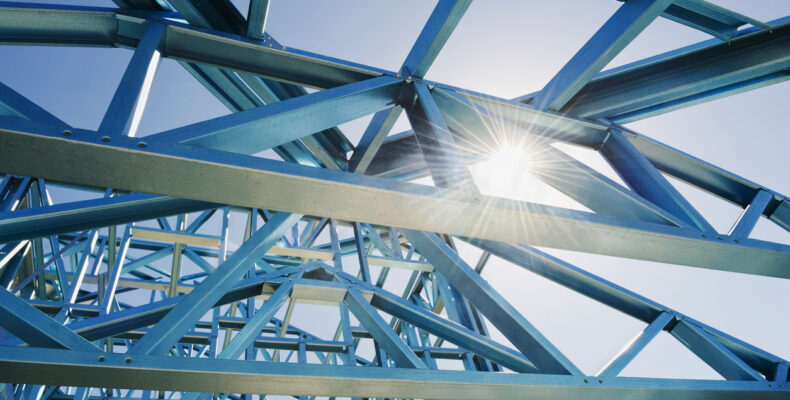
Firing up an industry: the science behind green steel
Steel production is responsible for more than 7% of global CO2 emissions, making it one of the world’s dirtiest industries.
A key step in the steelmaking process is reducing iron ore to extract iron – the raw material from which steel is made.
The traditional approach to reducing iron ore is to melt the iron ore with coke (a fuel derived from coal) in a blast furnace operating at over 1500°C. Carbon in the coke reacts with and extracts oxygen from the iron ore to leave molten iron. However, this process requires vast amounts of energy to reach the required temperatures and using coke as a reducing agent produces significant amounts of CO2.
An alternative approach is ‘Direct Reduction of Iron’ (DRI). DRI is a solid-state process that takes place below the melting temperature of iron. It involves heating iron ore in the presence of a reducing gas – typically methane or syngas (a mixture of carbon monoxide and hydrogen) – to extract oxygen from the iron ore to leave iron. While the lower temperature reduces the energy required compared to a blast furnace, the use of both methane and syngas still produces CO2.
DRI can also be carried out using hydrogen as the reducing gas. With hydrogen, however, the by-product of DRI is steam. As a result, CO2 emissions can be reduced by over 95% compared to coke-based reduction.
Hydrogen DRI in steelmaking is not new technology. However, hydrogen has historically been expensive to produce, providing a barrier to scaling up and developing hydrogen DRI to an industrial level.
In addition, unless the hydrogen used in DRI is produced cleanly with low or zero emissions (so-called ‘green’ hydrogen), the benefit of reducing CO2 emitted in the steelmaking process is counteracted by the CO2 emitted in hydrogen production.
However, with plenty of innovation in climate-motivated hydrogen production (electrolysis being the main focus), an increase in renewable energy production generally and various financial incentives across the world (including subsidies and tax breaks), the cost of producing green hydrogen has fallen significantly to the extent hydrogen-based products can now rival their fossil fuel-based alternatives on price.
The reduced cost of producing green hydrogen has greatly increased the viability of implementing hydrogen DRI in steelmaking at an industrial scale. Examples of this can be seen in Sweden where start-up H2 Green Steel is on course to produce commercial steel using hydrogen DRI by 2025, with the hydrogen produced locally using electrolysis powered by renewable sources.
The ability to produce steel on a commercial scale using hydrogen DRI should encourage a move toward hydrogen-based steelmaking more widely – particularly as an estimated 70% of steelworks globally (the majority of which rely on blast furnaces) are in need of repair or replacement before 2030. That in turn should create plenty of opportunity for steelmakers to improve and refine the hydrogen DRI process.
The above factors coupled with the global push for more sustainable steel production means patent protection for developments in hydrogen-based steelmaking will become increasingly valuable.
Barker Brettell has a dedicated energy sector group that can assist and advise you. If you have a steel production invention you would like to protect, do not hesitate to contact the author or your usual Barker Brettell attorney.